The complete and efficient solution to fully manage all production process phases, from document flows to inventory material, finished and semi-finished products entries.
Mago4 – Advanced Manufacturing
In order to achieve a well-organized production process, it is crucial to consider every single aspect of the cycle, forecasting all the possible situations and to make the appropriate adjustments on time. If you need an efficient but also flexible tool, meeting your specific requirements, Mago4 Advanced Manufacturing module is the solution that perfectly suits your needs.
BILL OF MATERIALS
Both Bill of Materials and Work Process Cycle have been designed to perfectly fulfill your needs and allow you to fully manage setting up times, work centers, families of machines, tools and any alternative phase. You can join a specific calendar to any work center, with its work shift schedule (only with Advanced Manufacturing module). In the BoM, for every item you can manage drawings history with their revision control.
MANUFACTURING ORDERS
The Manufacturing Order contains information such as the list of materials, work processes, production times and costs, and has been set to ensure you more flexibility.
It is an important document concerning all production cycle, from Launch to the final balance, and shall be flexible in order to meet all your needs. You can freely change the list of materials and work process phases to be executed, even when the order has already been entered, without changing its BoM definition or standard production cycle.
Thus, you can pick extra or different materials from the ones projected and easily set up reprocessing phases, with no need to redefine the standard product composition.
You can manually enter a manufacturing order, or let Mago4 automatically generate it starting from a production plan. In the latter case, the manufacturing orders are generated not only for finished but also for all semi-finished products that are on lower levels of the BoM.
With Manufacturing Planning or Advanced Manufacturing Planning modules you can originate the manufacturing orders starting from the consolidation of MRP Simulation or CRP scheduling procedure. When the order is generated, you can launch it in production picking the necessary materials and checking the availability in the storages enabled for this operation. This allows you to manage into the inventory the materials or semi-finished products that are not available for production since – for example – they still have to pass inspection phases.
PICKING LIST
You can print the document (Picking List) through which you can pick, and integrate it with information concerning, for example, the material lot and the source storage. If the availability in the listed storage does not cover requirements, you can indicate alternative storage for the unavailable quantities. Thus, the lack of one or more materials/components (perhaps actually available but not yet entered in the computer system) will not prevent production launch. When you launch an order in production, you can decide to automatically issue the picking list, perform the actual picking and generate outsourcing documents (if work is outsourced) or to execute those actions later, following specific procedures.
THE PRODUCTION CYCLE
The production cycle can start at this point. Using the Production Progress procedure you can decide which phases to send to production, according to the inventory material availability. The list of phases selected for a given order and/or on a work center, forms the Work processing List.
The works progress can be constantly monitored using special control reports, which report differences in projected and already completed work processing times and quantities. Even when work processing has already started, it is possible to change the assigned work center to deal with an urgent job or unavailability, for example.
The new work center can pass from in-house to outsourced or vice-versa, or the reference contractor may change. Mago4 reverses and regenerates the documents, even those related to outsourcing.
These operations are under maximum control thanks to a specific work-in-progress maintenance function. If data is incorrectly entered by the operator or if production strategies change, you can cancel or correct picked materials.
Another function of work correction allows you to cancel or to correct every balance, either of the entire Manufacturing Order or its single phases. During the final balance you can declare the Manufacturing Order phases are ended, fully or partially, loading the corresponding deposit or balance and using different selection possibilities. The final balance of work processes provides you with dates, quantities, work process times details. If the Manufacturing Planning module is not installed, and therefore you can not use the MRP/II procedure, you can anyway obtain materials re-supplying using the specific Purchase Orders generation option.
With Enterprise edition, using the Control Panel, you can graphically display production status and the documents created starting from a job order, a Manufacturing Order, or combination of both. The control panel is an interactive tool, easy to use, that allows you to perform several operations without ever accessing the menu of Mago4. For example, it is possible to launch the production or go on with its progress.
SUBCONTRACTING
The Advanced Manufacturing module makes it possible to consider the contractor as part of your own set of production resources, thus providing maximum freedom in the organization of the work cycles processes. So, in a single cycle you can find both in-house and outsourced work processing phases: each in-house phase can be performed by a different work centre and each outsourced phase can be executed by a different contractor.
Mago4 automatically recognizes the need for the contractor to prepare the necessary additional documents:
Supplier order for work processes to perform, Delivery notes to send components to process and Bill of Lading for the return of processed material. The documents are also prepared according to the work sequence. For example, if the two outsourced phases are consecutive and the supplier of the first phase directly sends the material to the second supplier, the Delivery note is not needed; instead, if the two phases are consecutive but the processed goods return to the company after the first process, then the Delivery note is necessary.
For each work processing phase you can choose how to draft the Delivery notes, selecting from the list of sent materials or description of the semi-finished goods obtained from previous work process; you can also automatically add notes taken from the production cycle and indicate the work process to complete as additional information.
Mago4 generates documents according to different grouping criteria (delivery period, job, etc.) and manages them in line with Sales, Purchases and Orders modules; in particular Mago4 manages price lists by quantity ranges and validity dates. Documents are different from those in sales and purchase cycle. From the Bill of Lading and Purchase Orders you can get account payable, drafted by contractor, completed and checked according to the standards. Material sent to outsourcers is loaded in a specific contractor storage area, to let you check outsourcing inventory in an accurate way.
The final balance of work processing phases is completed in the same way as entering a normal bill of lading: at the end of the record, the phases are collected, permitting partial returns, in quantities other than those agreed and indicating whether the returned item is a finished, semi-finished or eventually second rate, as result of imperfect working.
4 STRONG POINTS
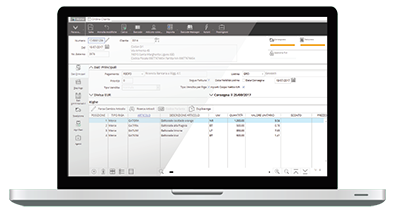